By Capt. Karl Anderson
Southern New Jersey is well known for its rich history of boat building. From the 1600’s on, with a virtually unlimited supply of cedar and oak, craftsmen built boats that were tools necessary for life on the Jersey coast, from seasonal inshore shallow water work boats like the “garvey,” to work the bay for clams and oysters among a host of other duties, and the incomparable Barnegat Bay sneakbox for gunning. Then a host of nearshore skiffs and offshore boats from bateaus to schooners to the four-chair charter boats and early walkaround boats also for hire. That ingrained necessity to create purpose-built boats has had a lasting impact on generations of South Jersey boat builders. Some of the earliest notable leisure boats were built just near the salty marsh of the creeks, rivers and bays that make South Jersey the unique gem she is.
Throughout the 1950’s, 60’s, 70’s and 80’s some of the most iconic brands in recreational boating and fishing came from these salty shores. Names like the Leek family’s Pacemaker and Egg Harbor Boats, Russell Post and his Post boats along with a host of other incredibly talented custom builders. These include Carl Adams’ Modern Boat Works, the Van Sant’s of Atlantic City, and of course Viking Yachts down on the Bass River, which continues to build a wide range of production boats for the sportfishing market.
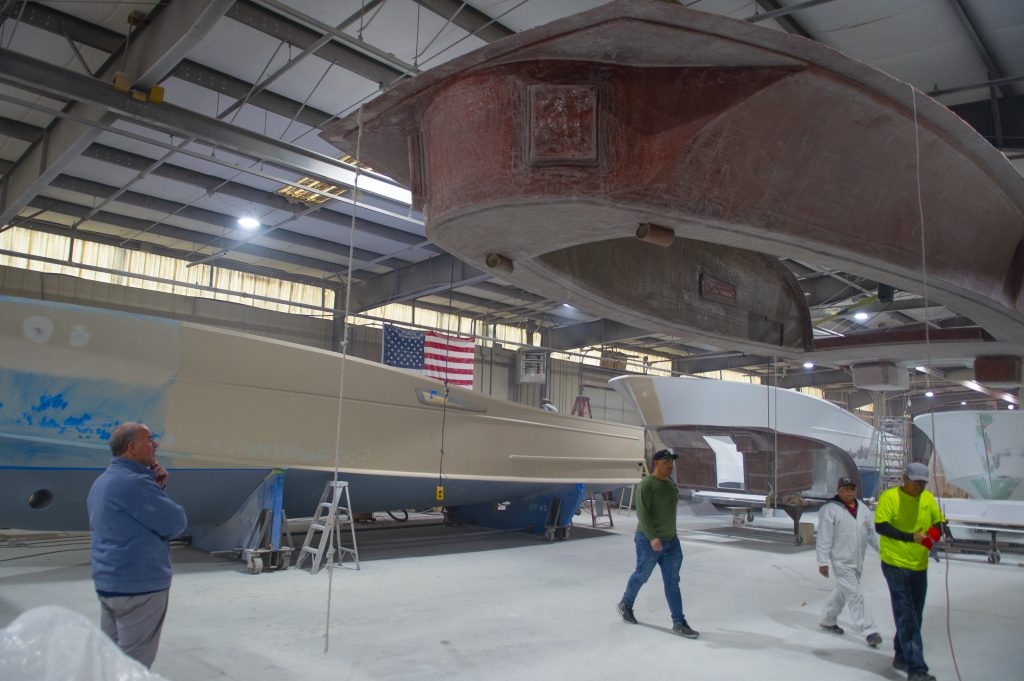
The Release Boatworks manufacturing facility sits in the cradle of this iconic boat building story. Interestingly, up into the 1950’s, all the many area builders were custom builders. The thriving charter fleets along the coast required well-built, durable boats to stand up to the seasonal and daily rigors of charter fishing. These craftsmen also had the call to build out the occasional yacht-grade sportfisherman or cruiser. Naturally, with the advent of modern materials like fiberglass resins and fabrics combined with molded construction and the increased power that became more readily available in diesel engines, the shift to production building pretty much shut down the custom builders of the day.
Today, Release Boatworks builds custom advanced composite boats to the whims of the owner while utilizing molded parts, a complete culmination of South Jersey’s rich tradition and modern technology. However, like anything built, it all starts with engineering. On a recent visit to the facility, I got to see first-hand how Release integrates technology to build a quality-focused boat. Release has assembled an in-house engineering staff that has a vast array of technology and tools to lead the various phases of the builds while managing the processes required to build high-end, custom sportfishing platforms. To start the product design and build process, the engineering team utilizes computer aided design programming to get two-dimensional drawings of the many pieces and parts required to make the boat. These are the foundation of the boat.
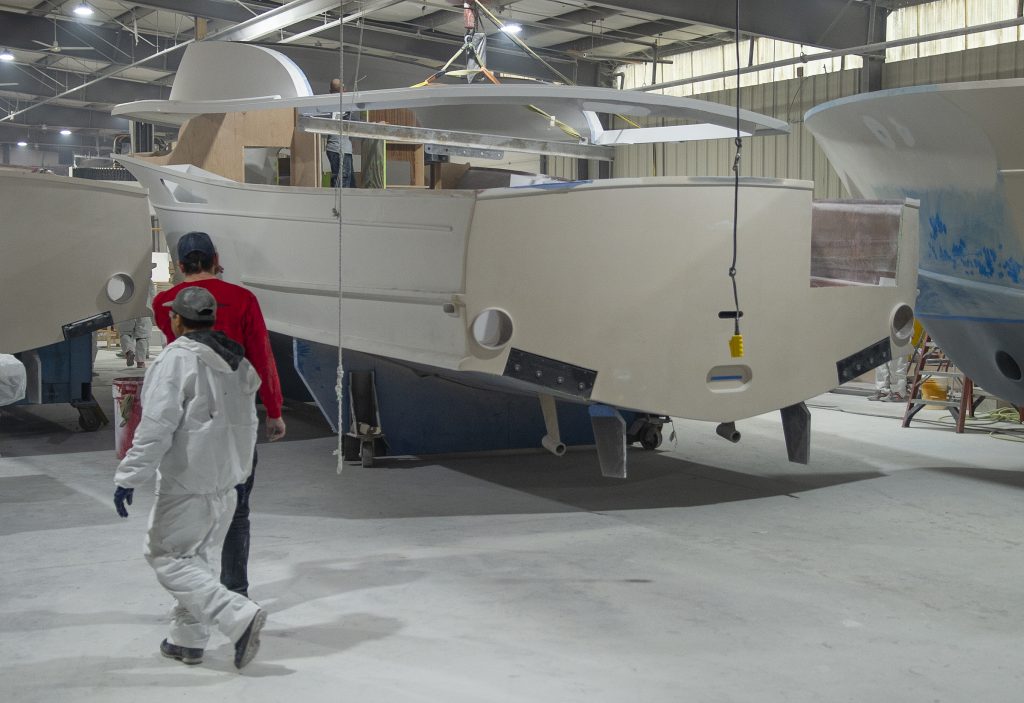
Going another step further, the use of Rhinoceros 3-D solid modeling software allows the staff to render spatial relationships throughout the boat while offering a fully rendered boat inside and out. The practical and proper positioning of equipment is essential to a well-functioning boat and further down the line in the boat’s life, allows for better long-term maintenance, a critically important consideration for any knowledgeable captain or owner.
All this information is then taken to another software program called Mastercam to be used on their C.R. Onsrud five-axis router to cut plugs that are used to create the molds. The router is only as good as the programmer’s input data, so this is where the CAD and Rhino phases of development offer their next greatest value.
The use of these software programs and the router, as in nearly every industry today, allow the manufacturer to pre-build the parts with incredible precision, resulting in cleaner, more accurate parts while also allowing engineering to fine-tune design and construction processes throughout the entire build. Having this forward vision gives the boatbuilder an accurate road map for the entire process. Ultimately, engineering the designs, materials and equipment into each boat reduces build time, errors, and increases quality.
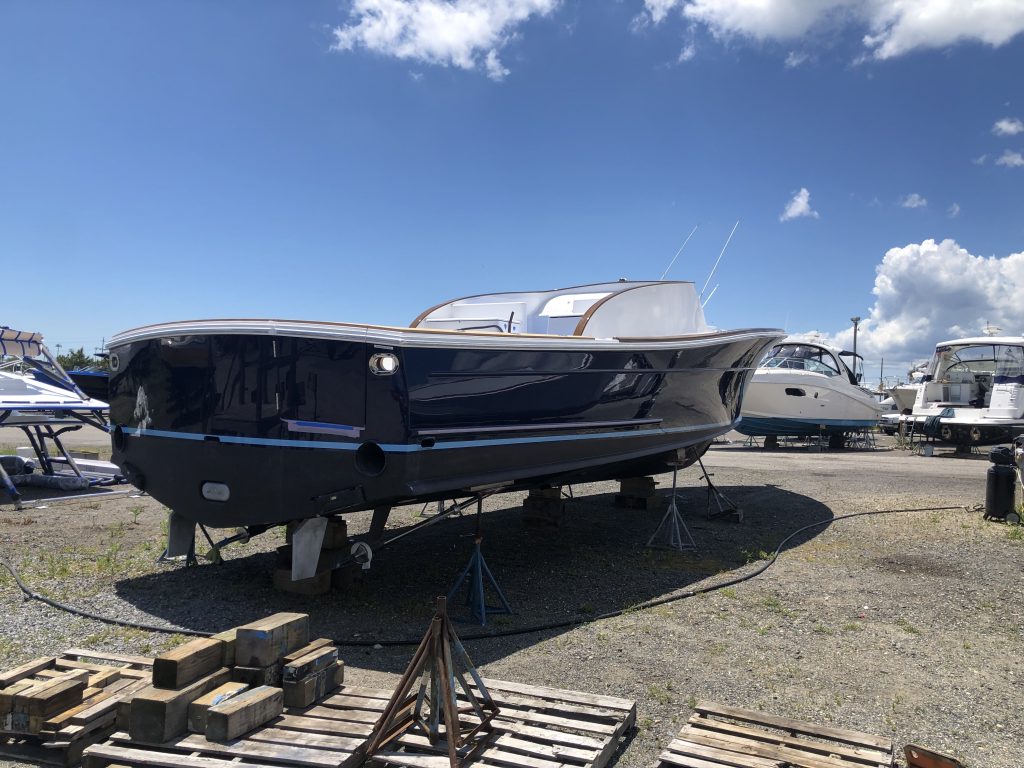
The use of molds decreases build time when compared to “stick building,” while also allowing for the use of the latest technologies for repeatable quality. The resin infusion and vacuum-bagging processes, coupled with cored composite construction, has proven time-and-again to not only be a more efficient build process, but renders a much stronger, tougher boat.
The advanced composite construction requires a complete engineering component all its own. Choosing a blend of fabrics of differing weights and fibers for certain places in the boat, and tailoring with sewn fabrics for strength, or finishing cloths, requires tight parameters to meet the demands of high-performance sportfishing boats. And various core thicknesses build shape and densities for strength, along with options for different core materials geared for certain qualities. Partnering with an industry leader in advanced composites, North American Composites (NAC), Release utilizes the specifications from NAC to set the standards on all build materials, while also training Release boatbuilders how to integrate them into the manufacturing process, as well as monitoring the build.
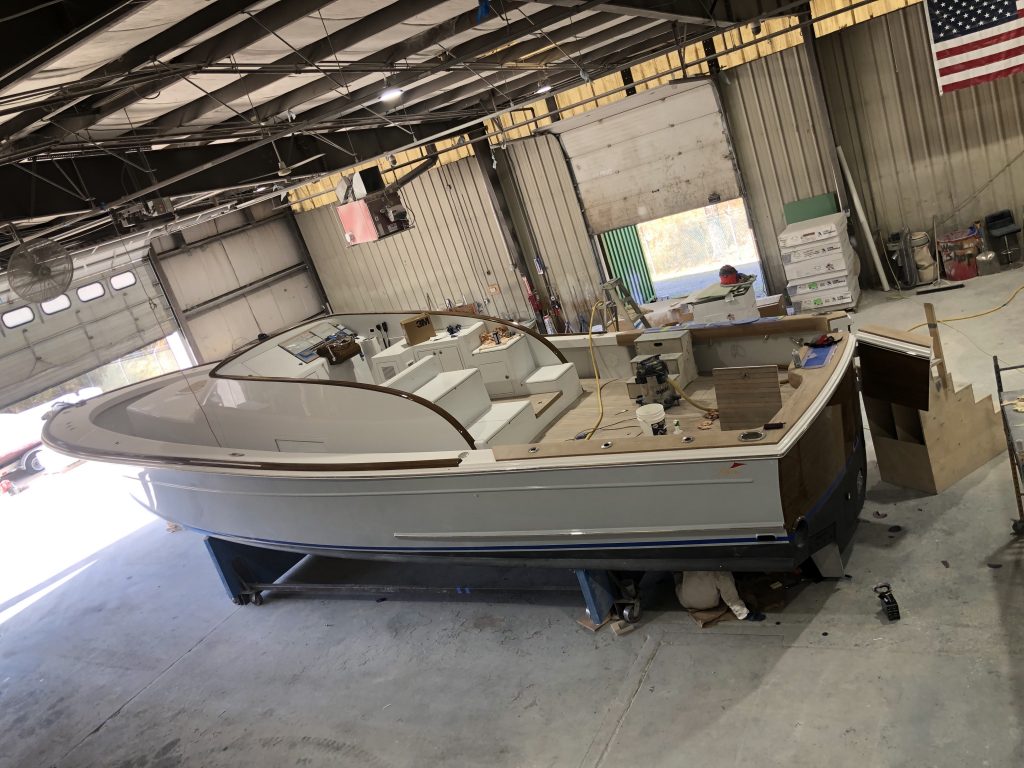
Once major parts like the hull, stringers, deck, house and for some models, bridge and console are made, they are then turned over to the boatbuilders to assemble and integrate core systems like plumbing and wiring. Along with major components including power plants, generators and the host of ancillary equipment like water makers, Seakeeper gyro stabilizers, ice machines, livewell systems and other items necessary to operate the boats, Release boatbuilders are fortunate to have the detailed engineering road map to lead them through the process.
Having been on several Release models over the years, from their first boat to the latest 43 Gameboat, as well as touring their manufacturing facility, I’ve been able to see their progression and evolution and realize the benefit that all the engineering, process refinement and focus on quality throughout has brought to their boats. With the flurry of recent deliveries from the fall of 2023 and spring of 2024, and a solid backlog, the builders at Release Boatworks will gain momentum and knowledge with every build and that all leads to a better boat. I’m looking forward to seeing the all-new 55 walk-around that’s coming soon. She’s sure to be a head turner!
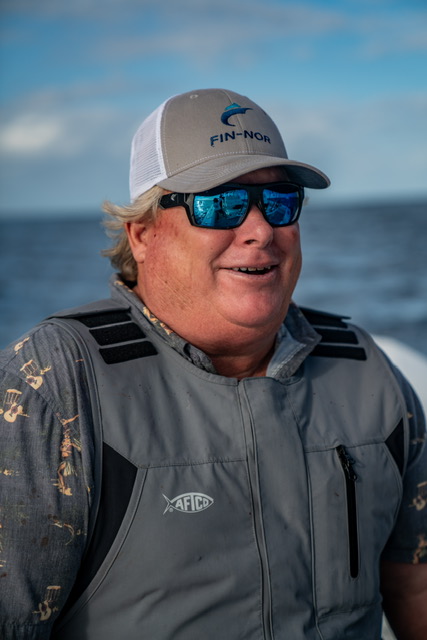
Capt. Karl Anderson has served as a senior editor and contributor to Salt Water Sportsman and Marlin magazines, and has written for Angler’s Journal, Yachting, Power & Motor Yacht magazines.
Anderson is an International Representative of the International Game Fish Association, Co-Chair of the Legendary Captains & Crew Award Committee of IGFA, and Chairman of the IGFA North American Council Rules & Recognition Committee. He is the recipient of the IGFA Tommy Gifford Legendary Captain & Crew Award.